Plastic extrusion for reinforced, resilient materials
Plastic extrusion for reinforced, resilient materials
Blog Article
A Comprehensive Overview to the Refine and Advantages of Plastic Extrusion
In the huge realm of production, plastic extrusion becomes a vital and very reliable process. Altering raw plastic into continual profiles, it caters to a variety of sectors with its amazing versatility. This overview intends to illuminate the detailed steps entailed in this approach, the sorts of plastic proper for extrusion, and the game-changing benefits it brings to the market. The occurring conversation guarantees to unfold the real-world influences of this transformative procedure.
Comprehending the Essentials of Plastic Extrusion
While it may appear complex at initial glimpse, the procedure of plastic extrusion is fundamentally basic - plastic extrusion. It is a high-volume production technique in which raw plastic is thawed and shaped right into a constant profile. The process starts with the feeding of plastic product, in the kind of granules, pellets, or powders, right into a warmed barrel. The plastic is then thawed making use of a mix of heat and shear, applied by a revolving screw. As soon as the molten plastic gets to completion of the barrel, it is compelled via a little opening referred to as a die, forming it right into a wanted form. The shaped plastic is then cooled down, solidified, and cut into preferred lengths, finishing the procedure.
The Technical Refine of Plastic Extrusion Explained
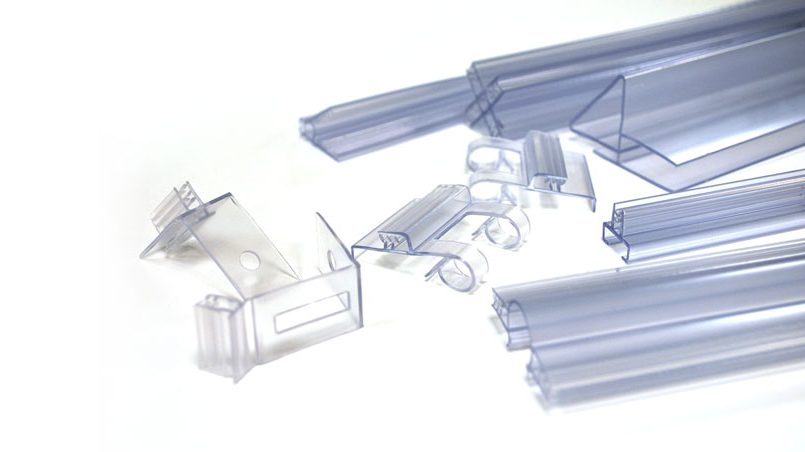
Sorts Of Plastic Suitable for Extrusion
The choice of the ideal kind of plastic is a critical aspect of the extrusion process. Different plastics use one-of-a-kind properties, making them much more matched to certain applications. Comprehending these plastic kinds can considerably enhance the extrusion procedure.
Comparing Plastic Extrusion to Other Plastic Forming Methods
Understanding the kinds of plastic appropriate for extrusion paves the way for a wider conversation on exactly how plastic extrusion compares to various other plastic developing techniques. These consist of shot molding, blow molding, and thermoforming. Each method has its distinct usages and benefits. Shot molding, as an example, is excellent for developing complex components, while strike molding is perfect for hollow things like bottles. Thermoforming excels at developing superficial or large components. Nevertheless, plastic extrusion is unparalleled when it involves developing continual accounts, such as gaskets, seals, and pipes. It additionally permits a constant cross-section along the length of the item. Thus, the option of method mostly depends upon the end-product needs and requirements.
Key Benefits of Plastic Extrusion in Manufacturing
In the realm of production, plastic extrusion offers many significant benefits. One remarkable advantage is the cost-effectiveness of the process, that makes it a financially appealing manufacturing approach. In addition, this technique gives premium product adaptability and enhanced manufacturing speed, therefore increasing total manufacturing efficiency.
Affordable Production Technique
Plastic extrusion leaps to the forefront as a cost-effective production approach in production. This process sticks out for its capability to produce high quantities of material promptly and successfully, supplying suppliers with considerable savings. The main price advantage is the capacity to make use of less costly basic materials. Extrusion uses polycarbonate materials, which are less pricey contrasted to ceramics or steels. Even more, the extrusion process itself is fairly straightforward, reducing labor prices. Additionally, plastic extrusion needs much less energy than traditional production methods, adding to lower operational costs. The procedure also minimizes waste, as any excess or malfunctioning products can be reused and recycled, supplying another layer of cost-effectiveness. In general, the financial benefits make plastic extrusion an extremely attractive choice in the manufacturing industry.

Superior Product Flexibility
Past the cost-effectiveness of plastic extrusion, an additional considerable benefit in manufacturing hinge on its premium product flexibility. This process enables the production of a vast array of products with differing styles, forms, and dimensions, from easy plastic sheets to complex profiles. The flexibility is attributed to the extrusion die, which can be personalized to produce the desired product layout. her comment is here This makes plastic extrusion a suitable option for industries that need tailored plastic components, such as auto, building and construction, and packaging. The ability to generate varied items is not just helpful in meeting specific market needs however additionally in enabling makers to explore brand-new product with minimal funding investment. In essence, plastic extrusion's product adaptability promotes advancement while boosting functional efficiency.
Enhanced Production Rate
A substantial benefit of plastic extrusion hinges on its improved production rate. This manufacturing process enables high-volume manufacturing in a reasonably short time period. It can producing long, continual plastic profiles, which significantly lowers the manufacturing time. This high-speed production is specifically useful in markets where huge amounts of plastic parts are required within tight target dates. Few various other manufacturing processes can match the rate of plastic extrusion. In addition, the ability to preserve constant high-speed manufacturing without giving up product top quality sets plastic extrusion apart from other approaches. The boosted manufacturing rate, for that reason, not only enables producers to satisfy high-demand orders however likewise adds to boosted efficiency and cost-effectiveness. This beneficial attribute of plastic extrusion has actually made site it a preferred selection in many industries.
Real-world Applications and Effects of Plastic Extrusion
In the world of production, the method of plastic extrusion holds profound value. The financial benefit of plastic extrusion, primarily its high-volume and economical output, has transformed manufacturing. The market is constantly making every effort for developments in recyclable and naturally degradable materials, suggesting a future where the benefits of plastic extrusion can be maintained without compromising environmental sustainability.
Final thought
In conclusion, plastic extrusion is a effective and very reliable approach of changing resources into diverse products. It supplies countless advantages over other plastic developing methods, including cost-effectiveness, high outcome, marginal waste, and layout adaptability. Its influence is exceptionally really felt in numerous industries such as construction, automobile, and consumer products, making it a crucial procedure in today's production landscape.
Diving deeper into the technological procedure of plastic extrusion, it begins with the option of the appropriate plastic product. As soon as cooled down, the plastic is cut right over here into the needed sizes or wound onto reels if the product is a plastic film or sheet - plastic extrusion. Comparing Plastic Extrusion to Other Plastic Forming Methods
Recognizing the kinds of plastic appropriate for extrusion leads the means for a more comprehensive discussion on how plastic extrusion stacks up versus various other plastic developing techniques. Few various other manufacturing processes can match the speed of plastic extrusion.
Report this page